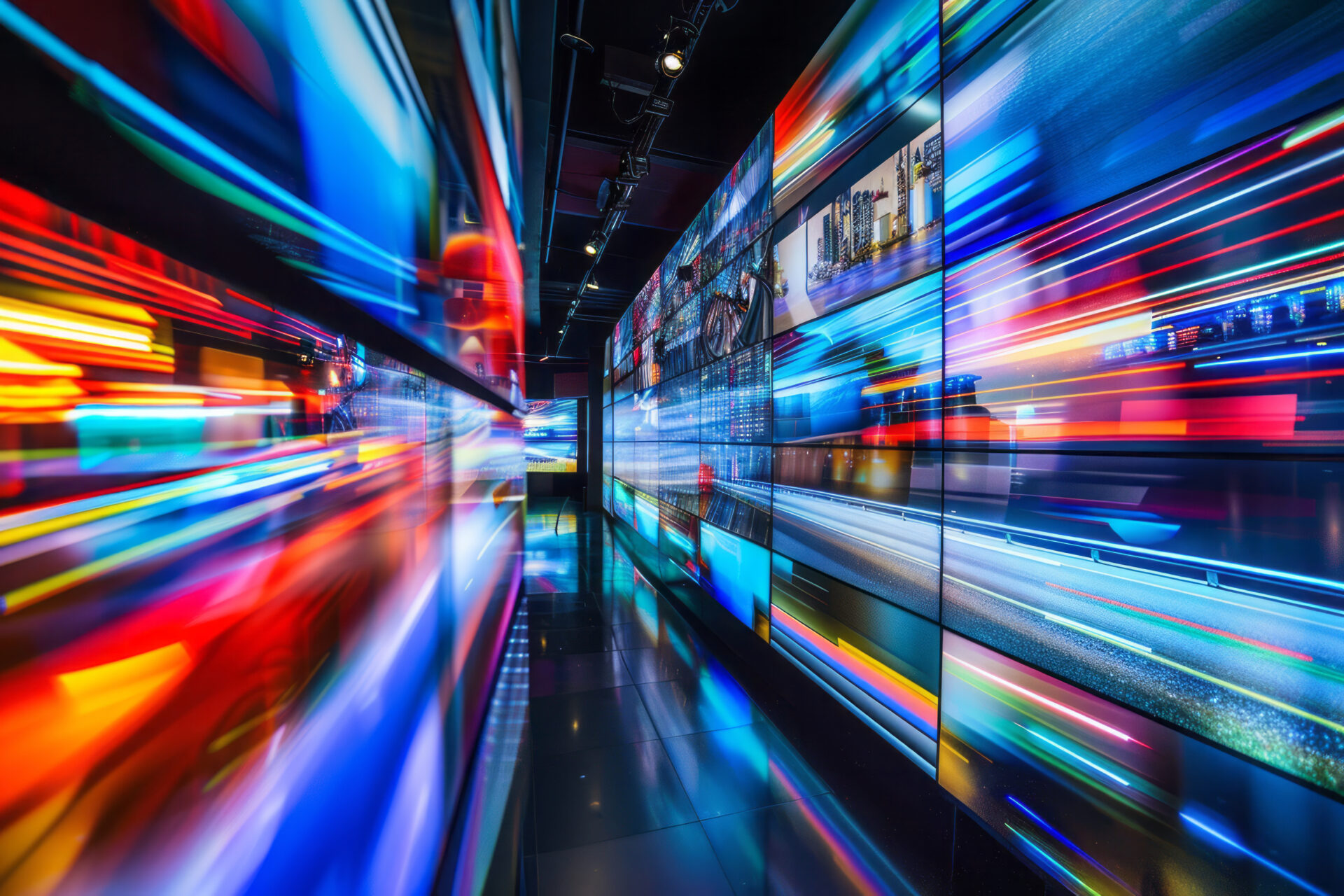
Newsroom
-
Braun Helps Indoor Billboard Rebuild After Devastating Fire
In July 2023, a devastating fire tore through Indoor Billboard’s laundry facility, bringing operations to a halt. Indoor Billboard partnered with other laundry operations to handle linen and mat processing during their recovery period. Faced with the massive challenge of rebuilding, they turned to G.A. Braun—not just as an equipment provider, but as a true…
-
Braun Honored with Awards at TRSA Industry Awards Dinner
GA Braun is proud to announce that it has been recognized at the TRSA Industry Awards Dinner with two prestigious honors: Best Video Award and the Advertising Effectiveness Award.
-
Braun Announces New Director of Aftermarket Operations
Braun is pleased to announce the promotion of Joseph Fiacchi to the position of Director of Aftermarket Operations, which became effective September 2024.
-
Safety at Every Step: Braun’s Integrated Approach to Project Management
Safety is integrated into every aspect of a Braun project. It is a consideration at every stage of project development and execution. Braun is committed to ensuring that all personnel remain safe during all project phases in laundry operations.
-
Science and Innovation Boosts Infection Control
Partner with OEM to optimize your processes In healthcare laundry, infection prevention starts long before clean linens reach the patient. It begins with a scientifically engineered, tightly controlled process that ensures soiled textiles are cleaned, disinfected, and returned free of microbial contamination. Partnering with an experienced OEM like Braun helps healthcare providers optimize their laundry…
-
Low Nox Dryers – Know Your Limits
Navigating Industrial Dryer Emissions Compliance in California and Beyond Tighter Air Emission Standards Are Changing How Industrial Laundries Operate California continues to lead the nation in environmental regulations, including some of the strictest air emission standards for industrial equipment. While most headlines focus on vehicle emissions, industrial laundry operators—particularly those in Southern California—face growing scrutiny…
Ready to get started? Let’s talk today.