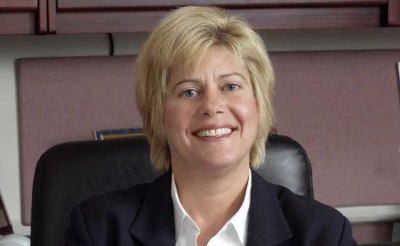
Article By: The Laundry Ledger
Braun’s Director of Marketing, Pamela Simonetti will retire on July 19th and Braun is welcoming Traci Anelli to her new role as Simonetti’s replacement.
As Braun’s Director of Marketing for 26 years, Simonetti was responsible for the development of the strategic planning and full tactical implementation of a wide variety of Marketing programs. They range from the company’s worldwide Corporate Communications Brand Management to advertising, eMarketing and digital platform programs, video production, publicity and public relations programs, and exhibit and conference management.
She is highly respected in our industry by customers, industry associations and other laundry equipment manufacturing professionals.
“I have been successful in managing my extensive portfolio of marketing efforts because I’ve had exceptional support from our engineering team, project management and service organizations,” says Simonetti. “Additionally, I’ve been fortunate to align with an effective external network of marketing communications support teams. I will always be grateful to the many people in the industry who helped me along over the years.”
Prior to Braun Pam served in several marketing and corporate communications positions within Eastman Kodak Company in Rochester, NY, NYC, NY, and Charlotte, NC. Simonetti plans on spending time with family, golfing, boating and enjoying her many other hobbies.
Simonetti is leaving Braun’s marketing programs in very capable hands. Taking the reins is Traci Anelli who joined the company as Director of Marketing in April, 2024.
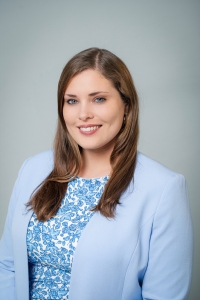
Anelli graduated from the State University of New York at Fredonia with a Bachelor of Science in Communications/Video Production. She studied journalism abroad at Bond University in Australia, and earned a Product Marketing certificate from Cornell University.
Before joining Braun Anelli was the U.S. Marketing & Communications Manager at Marquardt, a global leader in developing and manufacturing electromechanical and electronic switches and systems for the automotive, power tool, and home industries.
“I am honored to join Braun and lead the marketing efforts of such a respected, industry-leading company,” said Anelli. “Pam has set a high standard with her remarkable contributions over the past 26 years. While these are indeed big shoes to fill, I am eager to bring my experience and fresh perspective to the talented team at Braun. I look forward to building upon the strong foundation she established, driving innovative marketing strategies, and achieving new milestones for the company.”
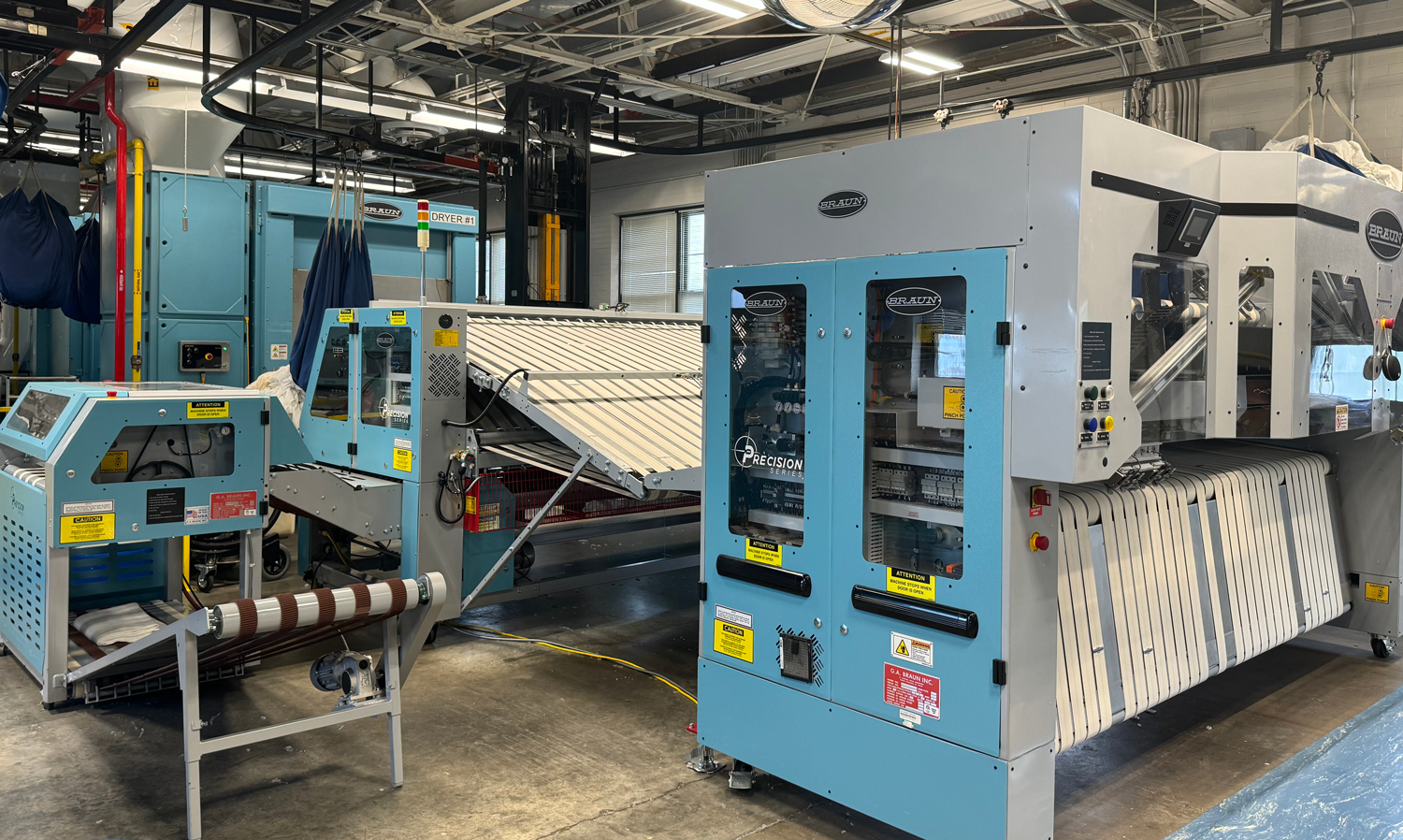
GA Braun recently completed a major renovation of an operational healthcare laundry facility in Upstate New York, upgrading key processing and finishing areas while maintaining full production throughout the project. This high-efficiency laundry upgrade demonstrates Braun’s proven ability to execute complex retrofits with precision, safety, and zero disruption to customer operations.
Scope of Work: End-to-End Equipment Replacement and System Modifications
The comprehensive renovation included:
- Complete replacement of wash deck equipment
- Modifications to the staph barrier wall for enhanced hygiene
- Clean rail system upgrades
- Blanket and small piece folding equipment replacements
On the wash deck, Braun installed:
- (1) Braun 800NMTDPV-6 Medicare Top Side Loading Washer/Extractor
- (2) Braun 400NMTVP-3 Medicare Top Side Loading Washer/Extractors
Utility connections for all new wash deck equipment were replaced with updated services. The original masonry staph barrier wall was removed, modified, and rebuilt with glass panels, improving visibility and maintaining sanitary separation.
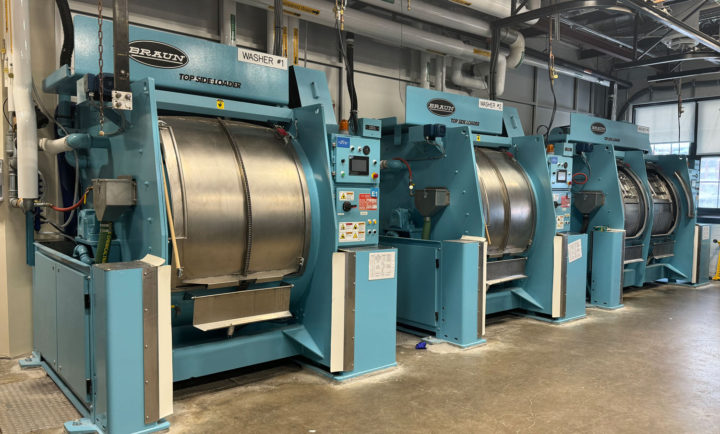
Finishing Area Enhancements for Healthcare Compliance and Throughput
On the clean side of the laundry, Braun installed a new high-capacity blanket system:
- Braun PSSF-130 Precision Series Spreader/Feeder
- Braun NIPF3CF/B-130 Precision Series Non-Iron Blanket Folder
- Braun BLPS-1 Precision Blanket Stacker
Additionally, two (2) Braun SPFRFM Precision Series Return-to-Feed Small Piece Folders were installed. To accommodate this finishing equipment, Braun rerouted and upgraded the clean rail system and provided all new utility connections.
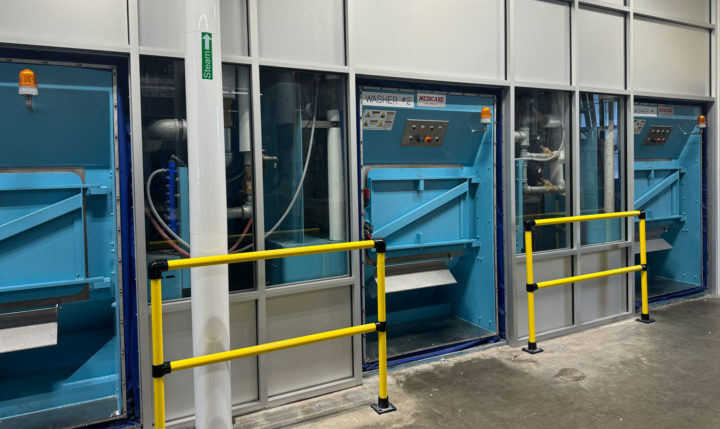
Phased Execution with No Interruption to Production
Maintaining full operational capacity throughout the renovation was a critical requirement due to the healthcare laundry’s role in servicing regional healthcare facilities. Braun developed and executed a phased installation schedule, performing work during off-hours and weekends to avoid any service disruptions.
Strict clean/soil separation protocols were enforced throughout the renovation, including during the replacement of the staph barrier wall, to ensure full hygiene compliance at all times.
Project Delivered On-Time and On-Budget
Thanks to strategic planning, close coordination with the healthcare laundry staff, and diligent collaboration with third-party contractors, Braun delivered the renovation on-time and within budget—meeting every performance and compliance benchmark.
“When Braun commits to an installation timeline and scope of work, we take great pride in our diligence, our proven procedures, and the resources that we leverage to complete our projects,” said Adam Thomas, Braun’s Technical Sales Manager. “From single equipment replacements to full plant retrofits, Braun will support all aspects of a customer’s laundry project.”
Need to Upgrade Your Healthcare Laundry Facility?
From efficient layouts to high-performance equipment and zero-downtime execution, GA Braun delivers full-service laundry renovations tailored to the healthcare sector.
Contact GA Braun today to start planning your facility upgrade.
Maximizing Efficiency and Capacity in a Landlocked Facility: A Braun Success Story
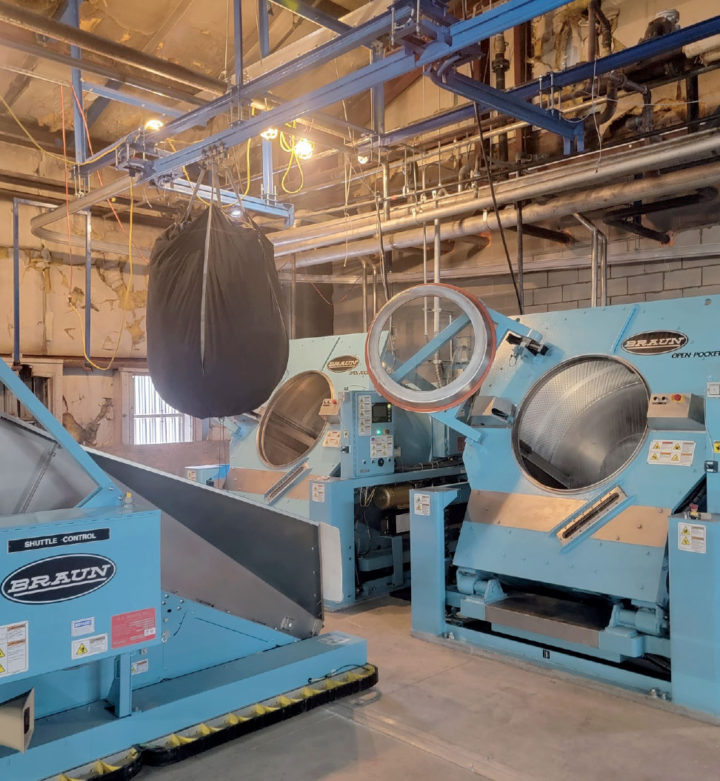
Maximizing Efficiency and Capacity in a Landlocked Laundry Facility: A Braun Success Story
In commercial laundry operations, maximizing efficiency and increasing capacity are critical to staying competitive—especially in space-constrained environments. That’s the challenge Braun’s Project Management Team tackled in partnership with Service Uniform at their Englewood, Colorado facility, located in one of the fastest-growing markets in the U.S.
With aging equipment and a facility boxed in by limited square footage, the Service Uniform plant needed to significantly increase throughput—without adding labor or relocating. Through a multi-phase strategic approach, Braun helped transform the site into a modern, automated production facility capable of handling nearly double the volume.
The Initial Challenge: A Landlocked Facility with Aging Equipment

When Braun began working with Service Uniform in 2018, the goal was clear: increase processing capacity despite physical limitations. During the initial site visit, Braun’s team evaluated the equipment layout, infrastructure, and potential expansion opportunities. One of the most impactful suggestions involved relocating the boiler room to free up valuable interior space.
A Strategic Upgrade Plan for Long-Term Efficiency
Braun developed a comprehensive facility upgrade plan that included:
- Up to five (5) Braun 450 lb. Open Pocket Washer/Extractors
- Three (3) 500 lb. Pass-Thru Dryers
- One (1) dryer bypass conveyor
- Braun OPSH Automated Shuttle System
- Clean goods takeaway conveyor
The layout allowed significant capacity growth within the existing footprint, reducing reliance on manual processes and maintaining current labor levels while preparing the plant for future expansion.
Automating the Wash Alley: Reducing Labor by 50%
Another major pain point was the original wash alley—a labor-intensive setup using six Braun washers and three non-Braun dryers. Braun proposed replacing five washers and integrating an automated shuttle system to optimize transfer times and labor usage.
Because the original dryers were not Braun models, the shuttle system required a custom design to ensure seamless integration. This upgrade, completed in Spring 2023, reduced labor in the wash alley by 50%, streamlining operations and increasing efficiency.
Project Management and Seamless Execution
Braun’s Senior Project Manager, Joshua Risewick, coordinated all aspects of the renovation—from equipment layouts and spec sheets to permit-ready architectural drawing packages. Working closely with contractors and Service Uniform’s internal team, Braun ensured:
- Timely equipment delivery and installation
- Minimal production disruptions
- Smart scheduling around daily operations
- Custom coordination with MEP contractors
“Through multiple phases and extremely detailed planning, we were able to integrate two Braun shuttle systems into a building where previously there had been none,” Risewick said.
Results: Increased Capacity, Reduced Labor, and Improved Workflow
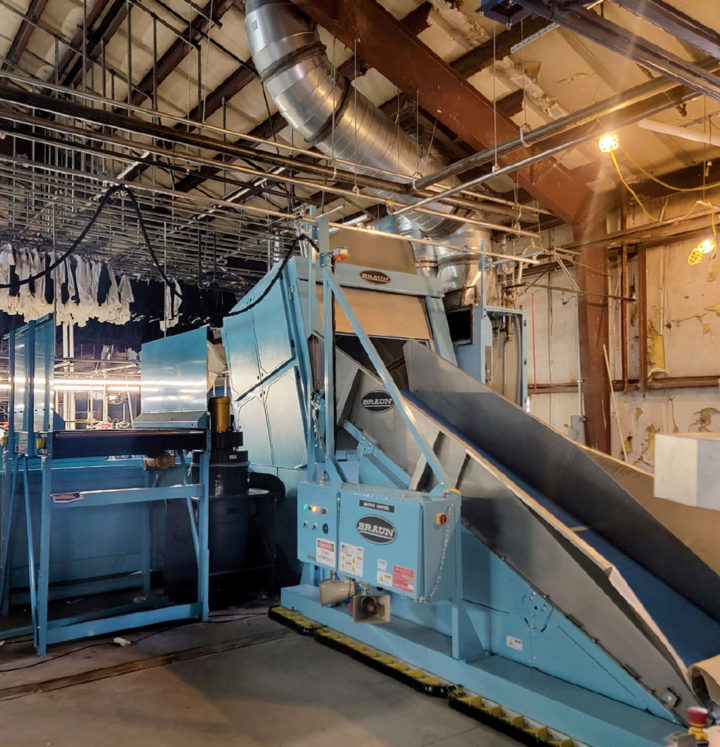
Thanks to Braun’s phased approach and use of high-efficiency equipment, Service Uniform realized several key benefits:
- Doubled wash capacity without expanding the building
- Improved workflow and reduced manual labor
- Faster transfer times and enhanced quality control
Dennis Tschida, Corporate General Manager at Service Uniform, shared this feedback:
“The new Braun open pocket washer/extractor system enhances labor efficiencies through its streamlined design and automation. Since the new equipment was installed, we’ve optimized our workflow and reduced manual tasks, improving overall productivity.”
“Braun’s commitment to excellence and collaboration has exceeded our expectations. We look forward to a continued partnership and future growth.”
Is Your Facility Landlocked But Ready to Grow?
Even in space-restricted environments, efficiency and capacity gains are possible with the right planning and equipment. GA Braun specializes in designing solutions for landlocked laundry operations—delivering custom layouts, automation, and project execution that maximize ROI.
Contact GA Braun today to explore how we can help reimagine your facility for greater throughput, efficiency, and success.
A fire destroyed a three-year-old Braun Triple Sort Small Piece Folder at Warrensburg Laundry (Warrensburg, NY). In just 8 weeks Braun delivered a brand-new folder to Warrensburg.
The triple sort folder plays a crucial role in efficiently processing bath sheets, towels, and incontinent pads. This small piece folder is designed to process and separate these items, ensuring that each customer receives the appropriate linens, optimizing workflow and enhancing overall quality and customer satisfaction.
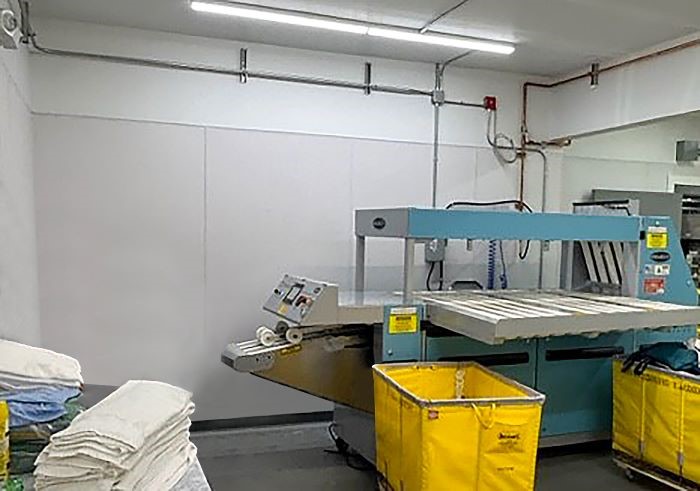
In the past decade, the population of Denver grew more than twice as fast as that of the U.S. While this meant expanded opportunities for area businesses, it also posed serious challenges for Service Uniform, which was maxing out its production capacity. This issue, coupled with rising labor costs and staff shortages, forced the company to reevaluate its business approach. Ultimately, Service Uniform decided to automate its wash alley with a new Braun Open Pocket Shuttle System. The automation significantly improved transfer times, resulting in greater efficiency with less labor. That, in turn, enabled Service Uniform to boost production to meet current and future demands.

Published in the May 2023 issue of American Laundry News.

There are three types of pre-owned equipment categories to consider when deciding on a piece of equipment not purchased new from the original manufacturer (OEM).
There is truly “used” equipment that is typically purchased “as is.” Second, there is the equipment purchased from a third party and then “rebuilt.”
Lastly, there is the equipment purchased from the OEM that is rebuilt to the OEM specifications and today’s standards of safety.
The key in each situation is to ask the right questions about the pre-owned equipment. Here are some important questions a buyer in this “as is” situation should try to answer:
How many hours of actual runtime does the machine have on it?
If more than 30,000-50,000 hours, it is likely approaching the end of its useful life without going through a complete rebuild. (Note: 30,000-50,000 hours = 14-24 years of runtime based on a 40-hour week.)
Was the machine purchased new, and why is it being sold?
A thorough inspection should be conducted. Look for any structural issues, evidence of poor maintenance or any functional issues. These are “buyer beware” signals.
Has the machine been maintained and are there records to support this?
No record of preventative maintenance presents a red flag.
Are replacement parts still available for the machine from the OEM or another source?
If not, this is another red flag … especially control parts for an upgrade or retrofit.
Certifications—does the machine have any certifications (i.e., UL, CSA, ETL) and will they remain valid if the machine is purchased and relocated?
Depending on the machine type, certifications could be mandatory by the local municipality in order to run the machine. Most certifications end when the machine is moved to a new location. Obtaining a new certification could be impossible.
Looking at a third-party rebuild? Here are some questions to ask:
Does the rebuilder have references on other like equipment that you can check on?
No references could mean poor workmanship, and the machine may have been repainted but not rebuilt.
Has the machine been completely torn down and inspected for structural issues and repaired as necessary?
If the answer is “no,” or “yes” with no proof, beware.
Are controls and components upgraded to the latest available or even able to be upgraded?
If not, are you able to get parts for what the rebuilder is selling on the machine? Are they obsolete?
Does the rebuilder provide a warranty on the rebuilt machine and components?
No warranty puts you back in the “as is” scenario. If a warranty is not offered, you need to know what is covered.
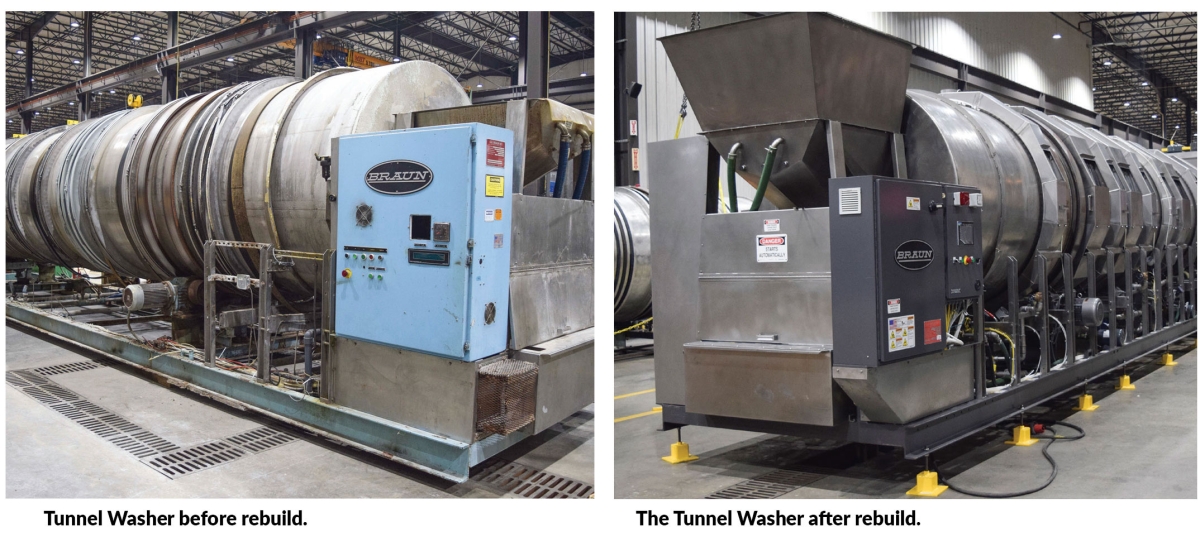
What certifications are necessary for you to operate the machine in your municipality?
CSA and ETL certifying agencies state that no rebuilder other than the OEM can re-certify a machine to CSA, UL, ETL or similar standards.
Does the third party offer aftermarket support?
If the third party outfitted the machine(s) with custom controls and/or parts, the OEM cannot help support the product when the machine breaks down and requires service. Often the changes that were made are not reversible.
Finally, if you are considering purchasing a rebuilt machine from the OEM, here are some questions to ask:
Does the OEM have references for similar equipment?
If the OEM cannot provide you with references on similar types of rebuilt equipment, that presents a red flag.
Was the machine completely torn down and inspected for structural issues and repaired as necessary? Does the OEM provide a warranty on the rebuilt machine?
If it was not, there’s a good chance that the warranty, if any, will be limited.
Were all components and controls updated to the latest available platform and updated safety features?
If they were not, can you obtain replacement parts in the future through the OEM or another source? If the answer is no, you have cause for concern.
Does the OEM offer service and technical support?
This is an obvious benefit for the long-term health of your investment. Whichever scenario you chose, take the time to do your homework and make sure a bargain is really a bargain.

Sandro Bortoloni, is director of aftermarket operations for G. A. Braun Inc.
Whether your laundry project involves a new building design, renovation, expansion or simply purchasing a new piece of equipment, the plant layout will need to be reviewed to keep the facility working at its optimum speed for the foreseeable future.
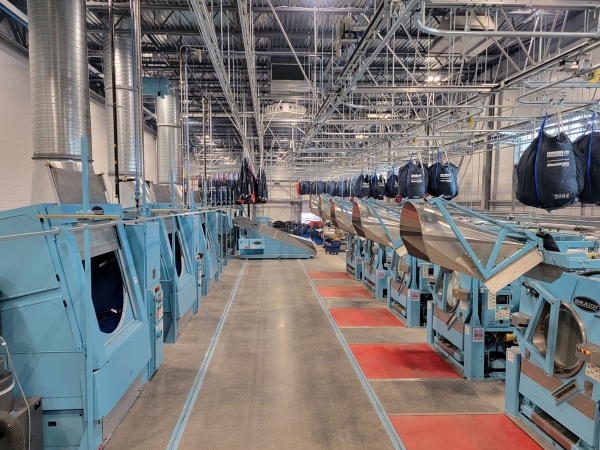
The design activity is key to review the material/process workflow but also validates existing utility and site infrastructure concerns for the project. In a perfect world, the equipment layout would begin with a ‘blank canvas’ and the concepts created by an architectural/engineering firm to design a laundry that best suits the needs of the customer. The optimization of the building space and utilization of the ‘cube’ would be taken into consideration to support the initial production processing volume as well as the strategic vision for business growth. Unfortunately, this ideal situation seldom occurs with laundry projects.
Most projects fall into the categories of expansion or renovation/retooling. These types of projects are the most complex given the need to maintain levels of production during project implementation activity. In some cases, a compromise must be made between supporting existing processing requirements and the project implementation. At Braun, we understand these unique challenges and partner with our clients to execute equipment installation projects in the safest and most cost-efficient manner.
During site assessments of existing facilities (whether it be healthcare, linen, or industrial plants), many operations are in older buildings with limited space to expand. Future expansion and strategic growth were likely not taken into consideration when the initial facility layout was completed.
Floor space is a precious commodity in a laundry. Yet, we discover batch tunnel washer systems set into building corners with no room to expand production capacity or replace aging equipment. Also, we find building additions that have been incorporated over time to accommodate new equipment to process additional capacity without considering process flow. Plants that have been expanded in this manner tend to resemble complex jigsaw puzzles.
Often these expansion efforts were not well positioned to support the needs of the operation strategically. Sometimes in the haste to address immediate equipment liabilities and/or process shortcomings, decisions are made that negatively impact the operation over time. This is why Braun believes in a thorough analysis and a comprehensive design approach in concert with the customer’s immediate processing requirements and future strategic vision. In this manner, all future business objectives are taken into consideration before implementing a solution.
It is important to place significant emphasis on designing processing solutions that will afford the operator the ability to grow the business without extensive capital expenditures for the concrete and steel necessary to construct additional operating space. Therefore, it is important to take into consideration strategic growth by allocating operating “space” for future equipment. Typically, Braun will illustrate future machines in the layout design as this approach provides a clear understanding where additional equipment is to be installed and integrated.
The majority of the time expended during the laundry design process is determining the current and future production requirements, the most efficient manner in which to process the goods, and the optimal fit of the equipment.
When designing a new facility, a number of criteria should be taken into consideration for a successful outcome. It is vital to understand the process flow of a facility, so equipment is placed in a configuration that optimizes material handling while allowing ample space for projected future expansion. An institutional laundry facility is no place for experimentation or guesswork. Not only has the Braun team accumulated decades of proactive experience, they’ve also embraced and shared the most innovative design tools and techniques. The use and knowledge of AutoCAD drawings and Building Information Modeling (BIM), plus other revolutionary approaches, will bring to life accurate buildouts of the proposed facility, supporting informed decisions about materials, capital expenditures and infrastructure – before the first shovel hits the ground.
Ceiling heights will need to be designed and specified with adequate above finished floor (AFF) clearance to accommodate monorail systems. Utility systems (electrical & mechanical) need to be provided for all necessary equipment and incorporate future growth needs in the design process. Chemicals, linen storage, loading docks, office space, maintenance areas (for equipment as well as fleet), employee locker rooms and rest rooms should also be taken into consideration with ample space provided. Parking and exterior access to the building for deliveries and material off-loading are often overlooked. This includes the routing and staging of various route trucks and large bulk transport vehicles on the facility property.
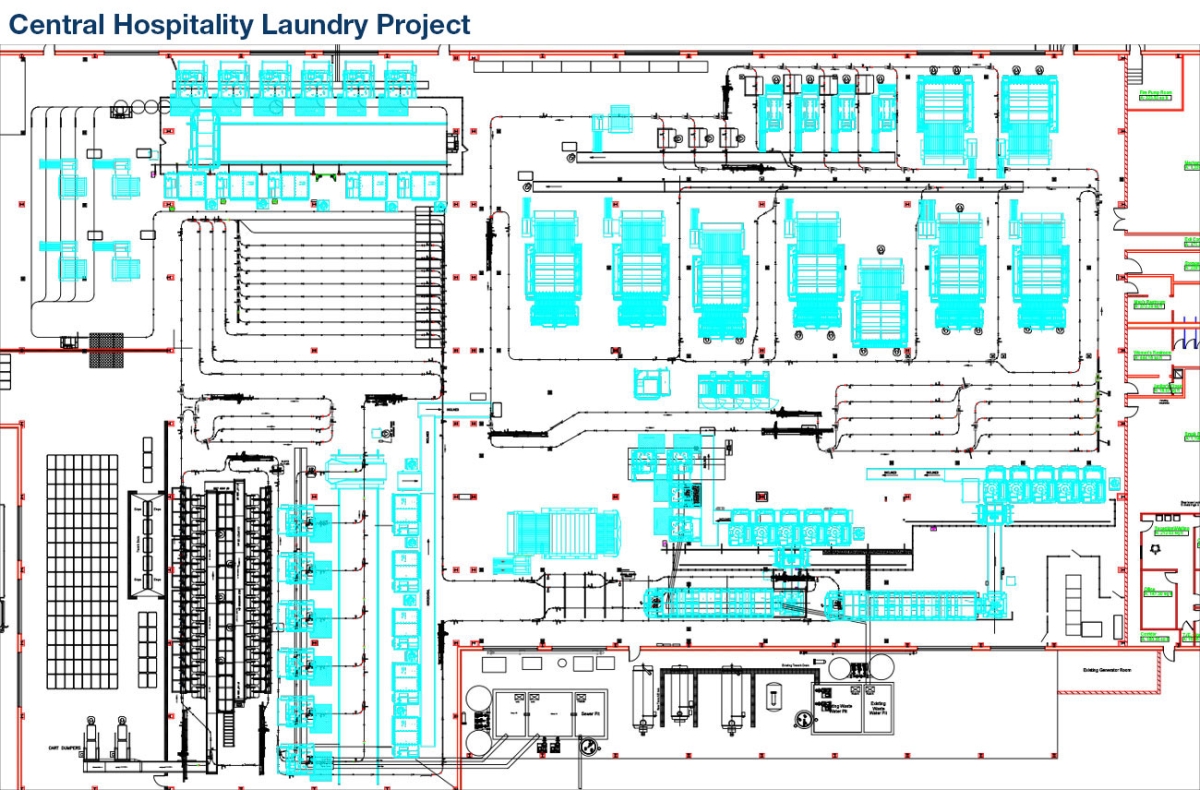
Customers are often looking for a solution to address their inability to meet production goals. Often, they simply want to add equipment to address this need. This may not always be the appropriate approach. Workflow may not be the first thing on a launderer’s mind, but it may be the answer to address their inability to meet goals. Analyzing the flow of goods in and out of a laundry plant, reviewing the production metrics and determining the equipment needed, along with incorporating material handling systems may be the best solution operationally, and this will undoubtedly be the best solution financially.
Increasing the automation level of an existing laundry facility certainly improves plant throughput. There has been an increase in customer interest to include more material handling with conveyors and monorail systems to reduce the number of carts; FTEs and non-value-adding handling. Braun has been partnering with third-party rail providers for more than 25 years for automated loading of batch tunnel washers and conventional washers. It is important to consider and review the potential to incorporate material handling solutions for clean goods which includes rail routing and staging to finished goods areas for flatwork and small piece processing.
These types of project submittals are key given the analytical details incorporated with the presentation materials so that the business owner can make important strategic decisions. It is also important to note that in most cases, many improvements are not completely captured in the ROI calculations. These include increased wash and finishing goods quality; better employee ergonomics; reduction in chemistry and potential reductions in linen replacement costs.
When you are choosing an equipment provider, your project will move smoother if the provider has the contacts and working relationship with suppliers from all aspects of your project build. Braun has the ability to partner with multiple 3rd party contractors ranging from general contracting companies to rail providers and process pipers to provide complete turn-key laundry projects.
Consider also that laundry re-tools require minimal machine downtime and extremely tight schedules. Through the use of tracking tools and the selection of qualified 3rd party partners, Braun has a proven track record of successfully executing these types and other types of projects – from single-point solution installations to on-premise facility projects, new construction of complete laundry plants and multiple system (BTW and Open Pocket) automated plants. Braun completes more than 150 projects annually in high-profile facilities across each market segments in the laundry industry.
If you select Braun as your equipment provider, our Project Management Team would work very closely with the laundry team in determining and completing the final scope of work for the project. Once the scope of work has been finalized, the Project Manager is responsible for the equipment layout drawings, foundation/trench detail drawings, equipment utility schedules, rigging plans, equipment installation details for MEP and any further submittal documentation required. Additionally, our Project Manager would interface directly with the retained architects, electrical and mechanical contractors, installation/rigging contractors, and utility systems engineers throughout the lifecycle of the project.
Our goal is to complete value adding projects on-time and on budget, safely and in line with the goals and expectations of our client partners. A successful project – with positive impact on the bottom line – demands strong partnerships with leading brands who provide meaningful support. For example, Braun is a time-tested laundry equipment manufacturer known for both world-class systems and stellar working relationships.
by Cliff Quick, Director of Inside Sales and Project Management and G.A. Braun Inc.
Process Optimization for New and Existing Dryers
Maximizing dryer performance and energy efficiency is critical for industrial laundries. While the industry has benefited from relatively low energy prices in recent years, optimizing the drying process remains essential for three key reasons:
- Market Trends: Fully drying linens is becoming increasingly common across key market segments: healthcare (80%), hospitality (55%), and food & beverage (40%). This trend is expected to continue as synthetic fabrics, which require specific drying conditions to maintain their integrity, gain popularity.
- Fabric Evolution: Synthetics retain less water after extraction, reducing energy consumption and drying times. However, they are highly sensitive to heat, and improper drying can significantly shorten linen life cycles.
- Future-Proofing: Even with low energy costs, optimizing drying processes helps facilities remain cost-efficient and better prepared for potential energy price fluctuations.
Key Mechanical Considerations
To optimize dryer performance, operators must first address external mechanical factors, whether upgrading existing equipment or installing new dryers.
1. Proper Ductwork for Exhaust and Intake
Improperly sized or installed ductwork is a leading cause of dryer inefficiency and increased energy usage. Poor airflow can also damage linens and create unsafe operating conditions. A simple manometer test can assess exhaust pressure:
- Ideal: 0.5 inches of water column or less
- Critical: Over 1.5 inches (operation should be stopped and airflow corrected)
Fresh air intakes also play a vital role. Facilities that seal garage doors in colder months may notice automatic door closures due to negative pressure. Introducing outside air can help regulate humidity, improving drying efficiency.
2. Proper Gas Sizing
Older dryers may operate at suboptimal gas pressure due to outdated designs, leading to inefficient performance. Ensure that dryers receive the correct gas pressure by consulting the owner’s manual or equipment nameplate, then working with manufacturers and contractors to confirm proper gas volume.
Key Factors in Dryer Performance
Beyond external mechanical elements, optimizing an existing dryer requires attention to internal components that directly affect drying times and energy consumption.
1. Minimize Ambient Air Infusion
Leaks in door seals, poorly designed dryer baskets, or substandard manufacturing tolerances allow ambient air to enter the drying chamber, disrupting the drying process. Modern dryers feature airtight doors and precisely placed seals to ensure air passes through the combustion chamber before reaching linens.
2. Airflow Engineering Improvements
Older dryer designs relied on manual engineering estimates rather than scientific airflow analysis. Today’s dryers use computational fluid dynamics (CFD) to optimize airflow, reducing drying times and energy use.
3. Maintain Combustion Blowers and Filters
In older dryers (10+ years), clogged filters can lead to poor gas-air mixtures, inefficient flames, and even dryer fires. Many modern dryers eliminate this filter, reducing maintenance needs.
4. Check and Replace Seals
All dryers use seals that wear over time. Newer models feature more durable, easily replaceable seals, reducing air leakage and improving efficiency.
5. Keep Blower Wheels Balanced and Clean
Blower wheels facilitate airflow. Over time, lint, dirt, and loose bolts can cause imbalance, reducing efficiency and increasing wear on components. Regular cleaning and belt maintenance prevent performance loss. Some newer designs use lint-shedding wheels to reduce debris buildup.
6. Monitor Dryer Cylinder Cleanliness
Coatings like Teflon or ceramics help keep dryer cylinders clean, but they wear over time. Avoid excessive heat or abrasive cleaning methods to extend their lifespan. New dry-particle removal systems provide fast, effective cylinder cleaning without damage.
7. Maintain Lint Collection Systems
Older dryers primarily used lint collection for air quality compliance. Today’s integrated lint systems are crucial for proper airflow and performance, protecting blower wheels and maintaining dryer efficiency.
Optimizing Burner Performance and Controls
While airflow is a dominant factor, burner efficiency, control systems, and proper operating practices also play a role in dryer performance.
1. Burner Health: Blue is Best
- Good: A blue flame indicates proper combustion.
- Bad: A yellow flame suggests clogged lint, incorrect fuel-air ratios, or the need for burner tuning.
2. Advanced Control Technology
Modern dryers adjust heat application based on linen moisture levels, minimizing fabric damage and shrinkage. This precision control ensures fabrics receive the least amount of heat necessary, improving textile longevity.
3. Proper Loading Practices
Loading a dryer to its stated capacity significantly impacts efficiency. Due to varying fabric densities, operators should fine-tune load weights for different classifications to maximize performance.
Final Thoughts
Drying efficiency is a science that requires careful attention to airflow, mechanical condition, burner performance, and load management. Industrial laundries should work closely with equipment manufacturers to implement best practices and ensure long-term dryer reliability and efficiency.
Need expert advice on optimizing your dryers? Contact GA Braun for tailored solutions to maximize performance and reduce operating costs.
Maximizing production throughput in an industrial laundry operation requires a proactive approach. Too often, operators focus on where a problem manifests rather than identifying upstream inefficiencies that create bottlenecks. Addressing these root causes can significantly enhance productivity, efficiency, and cost savings.
Washroom Challenges and Solutions
1. Soil Sorting and Load Management
The foundation of an efficient washroom begins with proper soil sorting. When materials aren’t staged correctly, it leads to underloaded machines, unpaired batches in tunnel washers, or empty pockets. These inefficiencies reduce capacity and disrupt downstream operations.
Prevention:
- Implement disciplined sorting practices to ensure full and balanced loads.
- Train staff on proper staging techniques to maximize equipment utilization.
2. Formula Management and Cycle Optimization
In conventional washing, modern machines offer significant flexibility to optimize both the wash and extraction processes. However, many operators don’t fully utilize these capabilities. On the tunnel washing side, there’s a common misconception that running shorter cycles (e.g., 90 seconds) increases throughput. In reality, optimal extraction requires sufficient high-pressure time—typically 60–75 seconds—to achieve the best water removal and efficiency.
Prevention:
- Work with OEMs to understand the full potential of your equipment’s extraction settings.
- Adjust cycle times to optimize drying efficiency and reduce conditioning needs.
3. Material Handling Delays
Many facilities struggle to keep up with unloading dryers and conveyors, leading to avoidable slowdowns. Often, this is a matter of operational discipline rather than a lack of capacity.
Prevention:
- Implement clear unloading procedures and accountability measures.
- Regularly evaluate workflow efficiency to identify and address bottlenecks.
Finishing Line Inefficiencies
1. Ironer Line Speeds and Boiler Capacity
Insufficient ironing line capacity can result from inadequate ironer size, insufficient surface contact pressure, or excessive moisture content in bypassed items.
Prevention:
- Ensure your ironers and boilers are adequately sized for your throughput.
- Optimize wash formulas to minimize unnecessary conditioning before ironing.
2. Manual Material Handling Bottlenecks
The finishing end of the process is labor-intensive, and inefficiencies in material handling can create costly slowdowns. Automation can provide substantial benefits but must be integrated thoughtfully to avoid introducing new bottlenecks.
Prevention:
- Evaluate automation options to streamline labor-intensive processes.
- Design automation solutions that align with your facility’s workflow and capacity.
3. Equipment Versatility and Product Mix Alignment
Many plants rely on specialized machines that can only process specific product types. Once those items are finished, the equipment sits idle, creating inefficiencies in labor, energy, and overall capacity.
Prevention:
- Invest in equipment that offers flexibility to handle a variety of product types.
- Continuously reassess your product mix and adjust processing strategies accordingly.
Final Thoughts
While every laundry operation has its unique challenges, these common problem areas often present the greatest opportunities for improvement. By focusing on upstream efficiencies, proper load management, optimized formulas, and effective material handling, facilities can significantly enhance throughput without unnecessary capital investment.
Taking a strategic approach to these operational areas will not only improve production flow but also reduce costs, save energy, and enhance overall efficiency. Looking for expert guidance? Consult with GA Braun to optimize your industrial laundry operations today.
Whether you’re designing a new laundry facility, renovating an existing plant, expanding operations, or installing new equipment, it’s crucial to approach layout and infrastructure planning strategically. A well-designed plant layout ensures smooth process flow, supports utility efficiency, and prepares your business for future growth.
Why Layout Planning Matters
In an ideal scenario, a new facility would begin as a blank slate. Architects and engineers would collaborate with the laundry operator to design a production environment optimized for current needs and long-term expansion. Unfortunately, most laundry projects fall into the categories of renovation or expansion—making them more complex due to the need to maintain ongoing operations during implementation.
At GA Braun, we understand these challenges and partner with clients to implement efficient, safe, and cost-effective equipment installation strategies. Our team helps design layouts that maintain production continuity while supporting strategic business objectives.
Common Challenges in Existing Facilities
Many healthcare, commercial, and industrial laundry operations function in older buildings with limited space and outdated layouts. Expansion often takes the form of patchwork additions, resulting in inefficient workflows and restricted equipment capacity.
We often find tunnel washers installed in building corners with no room for growth. These “jigsaw puzzle” layouts may solve short-term issues but can hinder long-term success. That’s why our approach emphasizes comprehensive design planning that includes:
- Space allocation for future equipment
- Optimal process flow
- Equipment flexibility
- Minimizing the need for future structural changes
Braun includes placeholders for future machines in layout renderings, helping clients visualize and prepare for scalable growth.
Key Design Considerations
Whether building new or renovating, every layout should support both current and future operations. Key planning elements include:
- Process Flow Optimization: Equipment should be arranged to minimize manual handling and support efficient material movement.
- Ceiling Height & AFF Clearance: Sufficient clearance is essential for monorail systems and overhead equipment.
- Utility Infrastructure: Design must support current equipment needs and future expansion in electrical, water, steam, and gas systems.
- Support Areas: Include dedicated spaces for chemical storage, linen storage, loading docks, office space, maintenance, employee facilities, and parking.
- Truck Access & Logistics: Ensure routes accommodate large transport and delivery vehicles.
Clients often approach us wanting to add equipment to boost production, but equipment alone may not solve underlying workflow issues. That’s why we begin by analyzing material flow, production metrics, and equipment interaction—often unlocking higher throughput without additional equipment.
Automation for Space and Labor Efficiency
Automation is key to improving efficiency and reducing labor costs in today’s competitive market. Braun has partnered with third-party rail providers for decades to implement automated solutions including:
- Monorail systems for tunnel and conventional washers
- Conveyors to reduce cart usage and manual handling
We’ve recently advanced this innovation with our patent-pending chute-loaded tunnel system dryer. This breakthrough allows automatic rail loading directly into the dryer via a static chute, reducing maintenance and mechanical complexity.
Benefits of chute-loaded dryers:
- Increased layout flexibility
- Reduced motion hazards
- Storage queue before dryers to eliminate scheduling delays
- Industry’s first true side-by-side dryer configuration, saving floor space
Strategic Planning and ROI
Successful laundry design is data-driven. Braun uses tracking tools and analytics to deliver turnkey projects that align with production goals and financial targets.
For example, in a recent healthcare laundry redesign, we proposed a strategic facility upgrade that improved production efficiency, reduced labor and utility costs, and modernized equipment. Here’s the return on investment breakdown:
- Estimated Project Cost: $898,032
- Annual Electrical Savings: $21,000
- BTW Maintenance Savings: $65,000
- Dryer Gas Savings: $10,819
- Ironer Gas Savings: $17,646
- Labor Savings: $279,864
- Total Annual Savings: $349,329
- ROI: 2.28 years
These results show how strategic facility planning and process optimization can deliver immediate and long-term value.
Why Partner with GA Braun
Braun has extensive experience in laundry plant renovations, new facility construction, automation integration, and high-efficiency equipment upgrades. Our project managers collaborate with your internal team, architects, contractors, and engineers to deliver scalable, cost-effective solutions—from concept to completion.
Let GA Braun help design your laundry operation for long-term growth, operational efficiency, and maximum ROI.